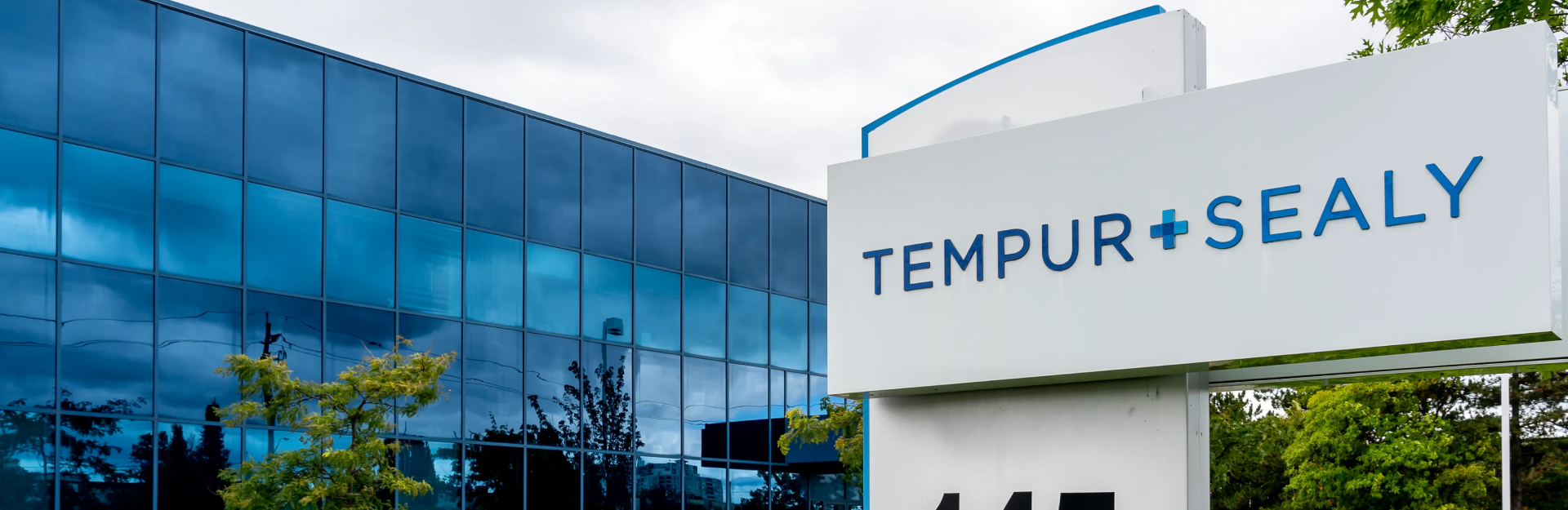
- Client: Tempur-Sealy
- Leadership: Lisa Nowak (Regional Vice President)
- Year: 2016
Overview
In 2016, our team led an initiative to integrate RFID technology into Tempur-Sealy’s Finished Goods inventory process. This project significantly enhanced operational efficiency, optimized product tracking, and fostered innovation across manufacturing and sales operations.
Challenges
- Lack of real-time visibility into the production and inventory lifecycle.
- Manual tracking methods leading to inefficiencies and inaccuracies
- Sales teams unable to quickly identify product manufacturing dates and locations, causing delays in customer support and order fulfillment.
Our Solution
To overcome these challenges, a comprehensive strategy to integrate RFID technology into the Finished Goods inventory process was implemented. This initiative was executed in close collaboration with Operations and Sales, ensuring seamless alignment with automation objectives and customer-facing requirements.
Key Achievements
Increased Automation:
- Enabled real-time tracking of inventory and production data.
- Reduced manual processes, saving time and minimizing errors.
Enhanced Product Visibility:
- Provided the Sales team with tools to accurately track when and where products were manufactured.
- Improved supply chain transparency, enhancing customer service and operational decision-making.
Strategic Framework:
- Conducted in-depth feasibility studies to ensure the project’s viability and alignment with business objectives.
- Developed detailed Project Charters to define scope, objectives, and stakeholder roles, facilitating seamless project execution.
Results
The successful integration of RFID technology streamlined inventory management while providing Sales and Operations teams with valuable real-time insights. This enhancement boosted overall productivity and elevated customer satisfaction.